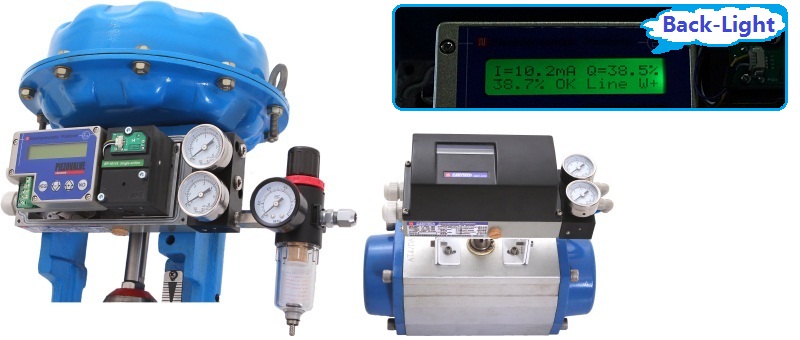
ESPOS Smart Electropneumatic Positioner Njetc, Njetc Việt Nam, Njetc VietNam, Njetc vietnam, Đại lý Njetc tại VietNam
Nhà cung cấp: pites
Hãng sản xuất: Njetc
ESPOS Smart Electropneumatic Positioner
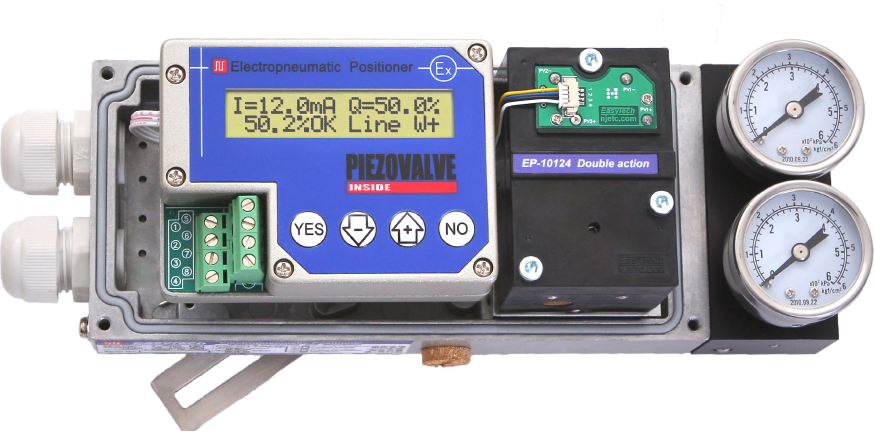
●Control process
The control algorithm of ESPOS positioner based on measuring process and data statistical analysis, the final control objective is quickly motion without any over-regulation.
Positioner would test all parameters such as pressure, response time, speed and acceleration; large step and fine step motion on a standard 25mm/2.4bar actuator before factory, this process was done twice under the conditions of elctronic open-loop and close-loop control and copy the data to MCU processor.
Above steps would do again when user initialize the control valve at appication field.
Positioner has two copies of data , the controller shoud analysis setpoint and actual position, according to the difference and acquired experience , microprocessor drive PWM signal to the piezo valves which regulate the flow of air into the actuator. The width of PWM increases or decreases according to the difference between setpoint and actual value.
MCU recorded the last 1024 periods control parameters at any time, the data will be refreshed every 40ms, positioner can determine exactly the next motion's direction and value, drive E/P a suitable signal to move actuator. The process repeated 12.5 times per second.
Positioner can also run adaptively when the variables changed such as compress pressure and flow increase or decrease, leakage of actuator, medium load pressure on pipeline, friction force on actuator pusher. The control algorithm has some artificial intelligence ability.
When the control valve in trouble, user analysis the data,factory-init, calibration-init, the last 30S record,solve problem as reference.
The positioner should timely record a typical data to non-volatile rom before breakdown.
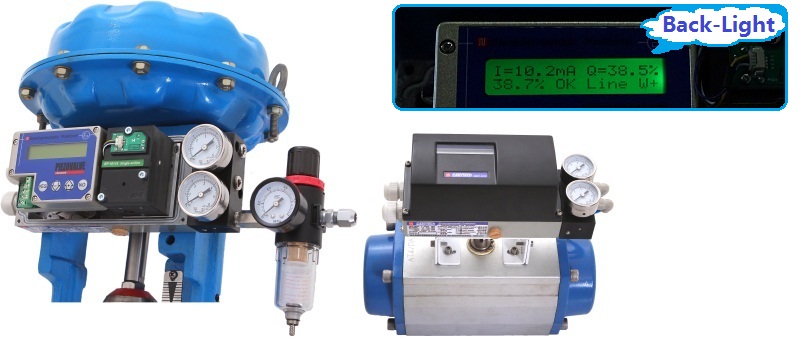
![]() |
![]() |
① Input signal ② Setpoint ③ + NC / - NO Actuator(If the feed-back lever direction towards right, reverse) ④ W Linear / T Rotary ⑤ Flow curve Linear / Free / Quick-open/ Quick-open Reverse ⑥ Difference of setpoint and actual |
|
1. Manual operation,by press UP DOWN 2. Sensor angle of initial position 3. Auto calibrate 4. Manual calibrate at 3 points (ZERO MID FULL) 5. Linear/Rotary optiones 6. Flow curve setting, 7. Setpoint direction ( 4-20mA/20-4mA) 8. Actual position direction ( 0-100%/100-0%) 9. Tightly close mode 10. Tightly close value set 11. Input signal range split 12. Sensibility setting, increase the value when actuator vibration 13. Sine curve compensate when feed-back lever not horizontal at 50% position 14. 2 chanels lited swich setting, change value for 8 output modes 15. Load factory setting 17. Actual position feed back direction ( 4-20mA/20-4mA ) |
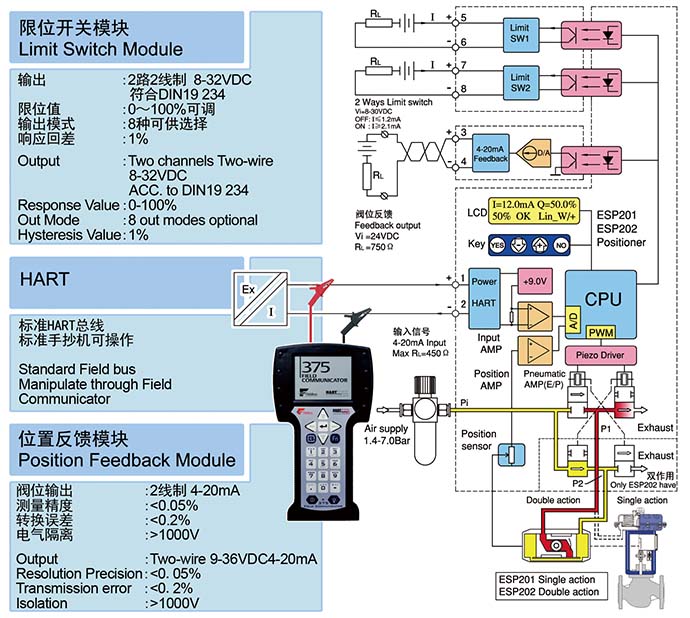
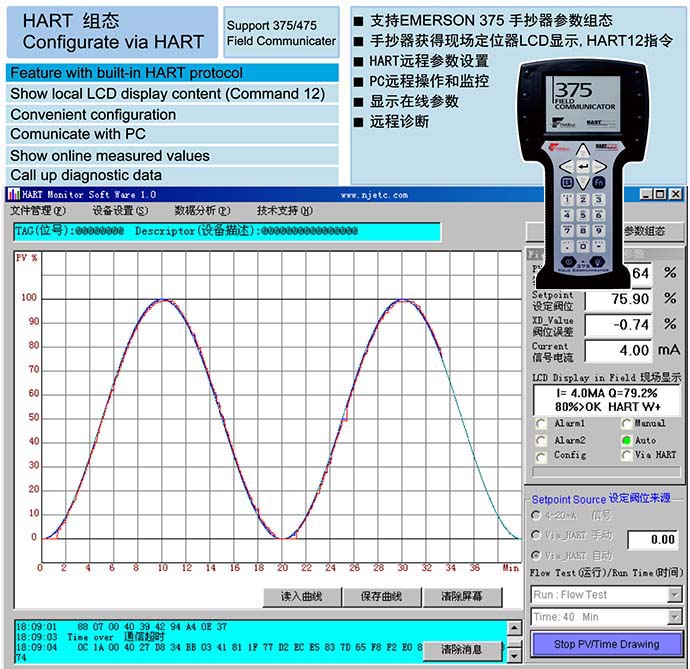
![]() |
User intialization: Open-loop accuracy +B1=Inlet -B2=Exhaust , Close-Loop accuracy +S1=Inlet -S2=Exhaust |
![]() |
![]() |
|
Press Hot-key YES display Close-loop Initialization +S1=Sensibility for inlet -S2=Sensibility for inlet
Open-loop Initialization +B1=Sensibility for exhaust
-B2=Sensibility for exhaust
|
Press Hot-key NO display 456=Inlet PWM time of standard valve 528=Inlet PWM time of user valve init. 536=Inlet PWM time of current 624=Exhaust PWM time of standard valve 664=Exhaust PWM time of user valve init. 680=Exhaust PWM time of current 536/680 Determine by the previous 1024 date for 30S. it refreshed 12.5 times per second. PWM time=N*30.52µS |
|
Please calibrate by manual when valve without limted block or turn angle >92° STEP1 Detect the actuator direction rise/fall STEP2 Dectect the ZERO point STEP3 Detect the FULL position STEP4 Time of exhaust (100% to 5%) STEP5 Time of full (0% to 95%) STEP5.1 Quick motion for inlet, Time/Speed/Over-control value STEP5.2 Fine regulation for inlet, get the suitable PWM time STEP5.3 Leakage measure, it will break when leakage value over 0.8%/S STEP5.4 Fine motion for exhaust, get the suitable PWM time STEP5.5 Quick motion for exhaust, Time/Speed/Over-control value STEP6 Test valve trval to 0-25%-50%-75%-100%-75%-50%-25%-0%. Display the hysteresis value. STEP7 Finish, press YES to save Display the error information when init. break. |
How to calibrate: MENU (2. Sensor angle? ) / (4. M_calibrate ?) / (12.Sensibility) |
Pneumatic Characteristics | ESPOS Ordering information and description | |||
Parameter | Symbol | Unit | Description | ESPOS38①-②-③④⑤ ① 1 Single acting
2 Double acting ② 0 Faile Safe A Fali in Place ③ F 4-20mA Feedback 0 None ④ L Limted Switch 0 None ⑤ H HART Module 0 None Please on request about ESPOS38X-A-XXX Fail in plce |
Supply pressure | Min/Max | bar | 1.4-7.0 | |
Output pressure | Min/Max | bar | 0 to Source pressure-0.1 | |
Flow | Qn | l/min | 130@6bar | |
Medium | Filtered air @30µM | |||
no or minimal oil | ||||
(max 30mg/m³) | ||||
Air Consumption | <0.006Nm³/h | |||
Safe position | Fail safe / Fail in place | |||
Temperature range | Min/Max | ℃ | -30 to 60 | |
Electrical Characteristics | ||||
Input signal | I | mA | 4-20mA, Two-wire Min 3.5mA |
|
Load resistance | R | Ω | <550 | |
Load voltage | V | V | 11.0 @4-8mA 9.0 @8-20mA |
|
HART Version | Universal 5 | Installation size | ||
Response time | T | mS | 80 | ![]() |
Feed back module | ||||
Power supply | V | V | 9-36DC | |
Output signal | I | mA | 4-20mA, Two-wire | |
Isolation voltage | V | V | 500 | |
Two channeles limted switch | ||||
Power supply | V | V | 8-32, Two-wire | |
Limted SW output | mA | ON:<1.2 OFF:>2.1 | ||
Isolation voltage | V | V | 500 | |
Ex-proof | ||||
Intrinsically-safe | ExiallCT6 Ga | |||
Mechanical Parameters | ||||
Dimensions | mm | 220x83x90 | ||
Weight | kg | 1.9 | ||
Body material | Aluminium alloy |
●Installing Accessory
![]() |
![]() |
![]() |
|||
Single | Double | 16-60mm | 16-110mm | ||
![]() |
![]() |
![]() |
|||
PA007 Mounting Board | PA008 lever Axis | PA009 Mounting kit for Rotory |
●Special Versions
Stainless steel housing positioner on request
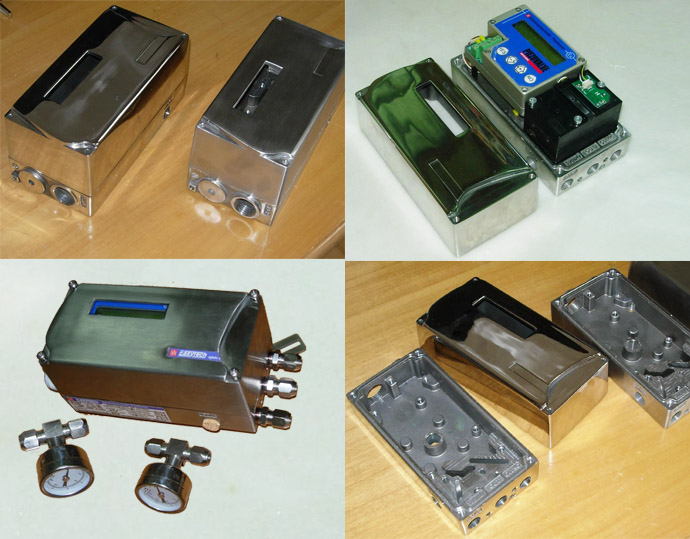